
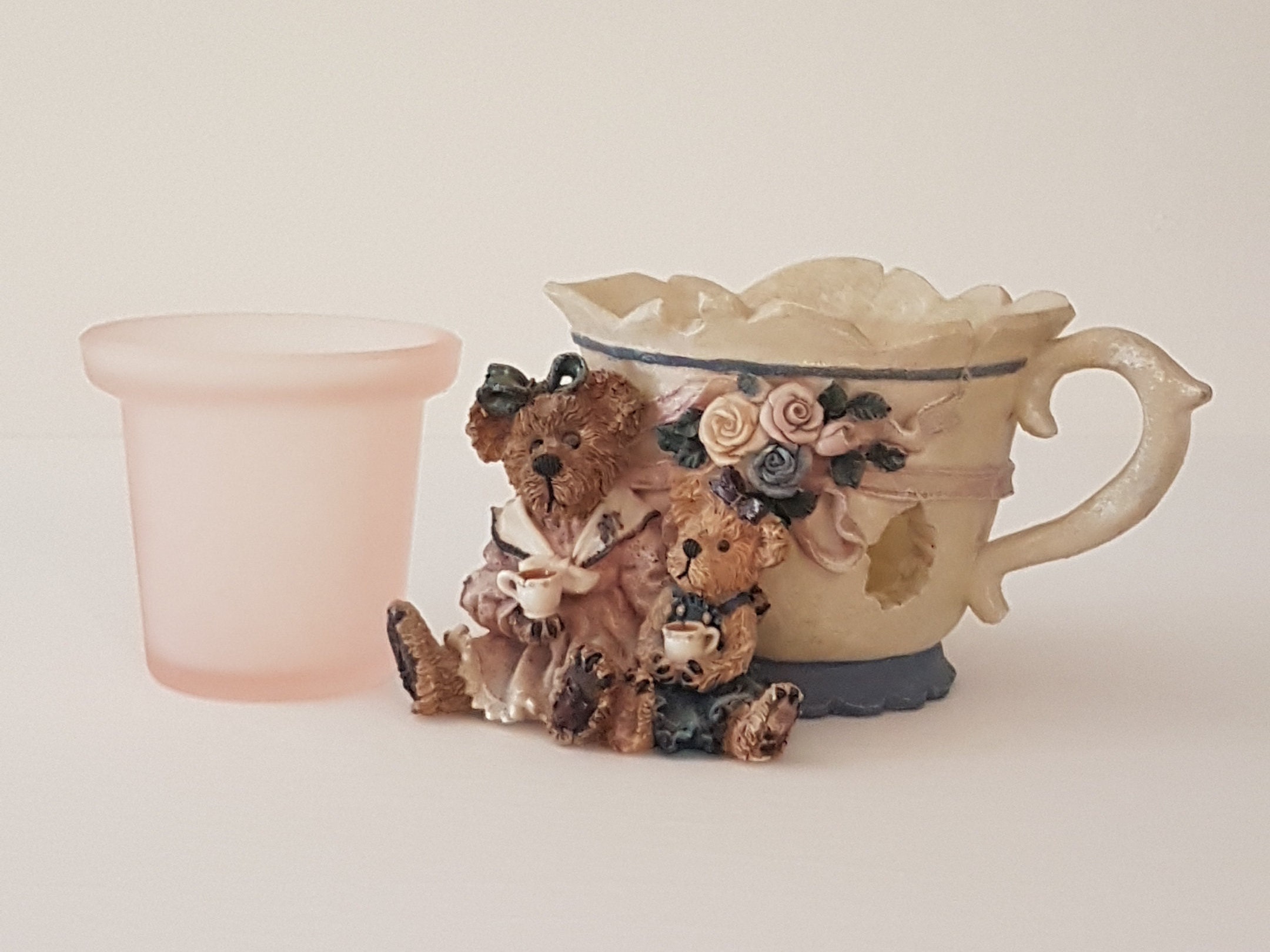
His skill of glass blowing is admired and ranked among the most beautiful in our nation. He has always been one of the few recognized true glass artists of our time. He still manages all this today and raised three children with his wife Roberta. He ended up in Cedarville IL and became a one man business, doing all his glass items, running his business and traveling worldwide. that had an abundance of natural gas to run his furnaces. He searched out the most central area of the U.S. He soon decided to venture out on his own. In 1973, he was employed by Fenton Art Glass Company to develop a contemporary glass product line. During this time he was asked by the State of West Virginia to become their resident glassblower. In a few short years he had developed his skill so well that in 1971 he left teaching and began traveling worldwide as an apprentice in several companies.
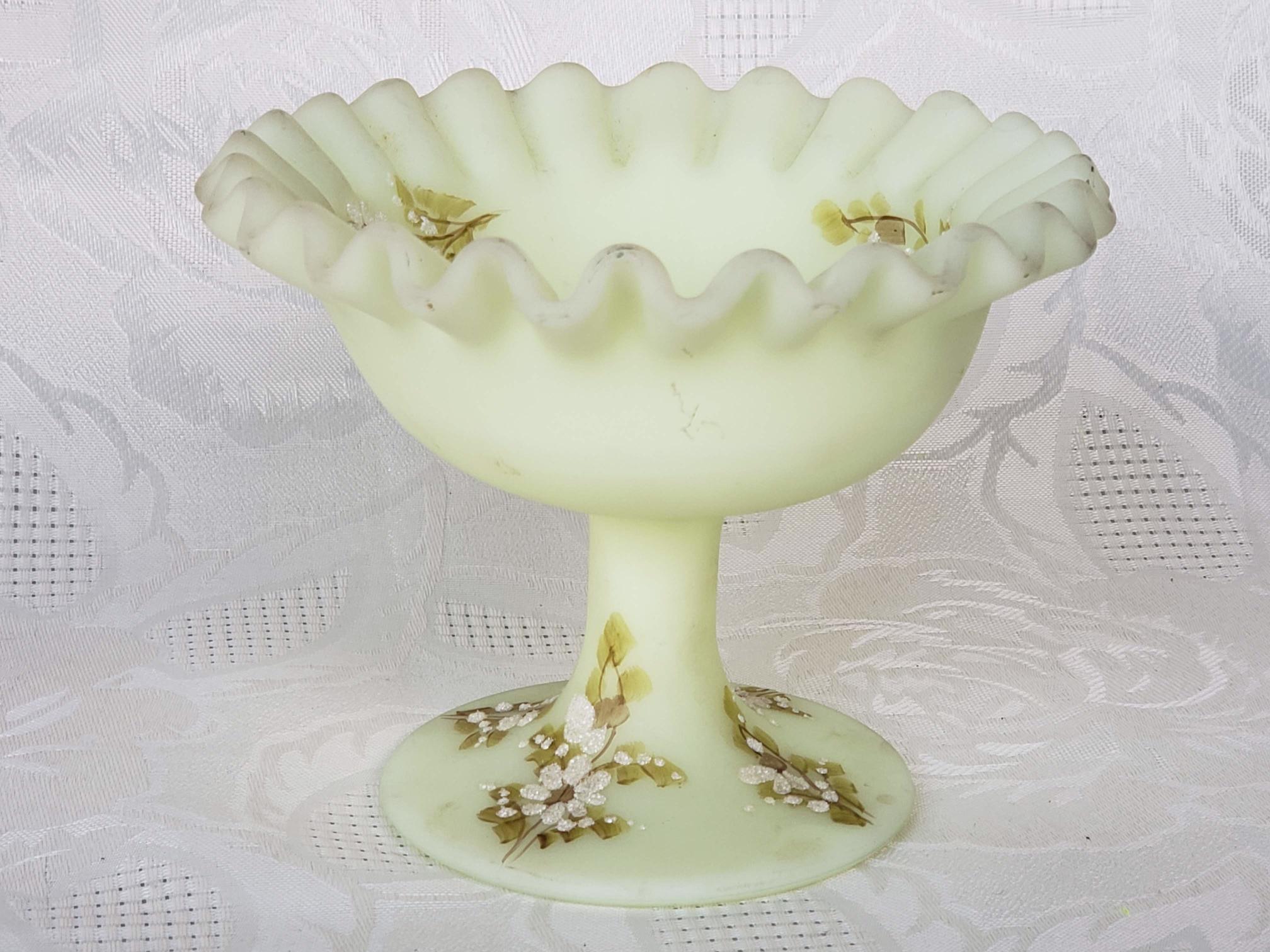
On his return he set up a studio where he could teach glassblowing as a course on campus. He was still so intrigued with the art of glass making, that in 1968 he took his pottery students on a trip to a glassblowing studio in Rochester, MN. He later developed an interest in architectural history which introduced pottery into his life. When offered an engineering scholarship to the University of Illinois he decided instead to attend the University of Northern Iowa, where he devoted his studies to the arts. However there are still people who are trying to keep this artesian art alive.ĭaniel Edler, now in his 60’s, is one of these people. Many of our glass objects today are mass produced. However, as with many of our antiques and collectables the age of machinery has put a huge dent in the world of glass. Thank you for being a part of our adventure.Is the art of glass making a dying business? For thousands of years master craftsmen have made beautiful one-of-a-kind pieces of glass items, from decorated figurines to vases, plates and actual drinking vessels. Glassmaking has been the most rewarding time of our lives. Our glassware will find its way into new collectors’ hands. We’ve never sold “seconds” and we’re proud of the legacy we continued. We are in reasonably good health for our age, but we’re mindful of what we must do to remain healthy. Our moulds have found a new home, without our signature Diamond B mark some tools have arrived in glass classrooms in universities and private studios.

For a man who’s always used his hands for work, I can boast that I have an iPad and can keep abreast of the day’s events.

#BOYDS BEARS HAND BLOWN GLASS HOW TO#
We will learn how to maneuver around the latest technology. We will read books and talk with friends. We’ll catch the late day’s sun rays as they filter onto our backyard deck. I was able to work alongside my father for ten years, work alongside my son for 32 years, and with my supportive wife for 59 years. We’ve welcomed visitors to our showroom, built lifelong relationships with our dealers and forged strong bonds with avid Boyd Glass collectors. Sue and I look forward to spending more time enjoying our family, walking on beaches, and gardening in our yard. Parenting is a career, so owning Boyd Glass made this our third career. During those years, we raised two children. I started out as a barber and Sue worked in the produce department with the Kroger Company. For four generations, the Boyd Family practiced the art of pressed glass making and passing their family formulas for glass colors down from father to son.īoyd Glass enjoyed 36 years of successful glassmaking.
